What are the three types of bonding failure?
In the adhesives industry, bond failures can’t always be attributed to a single factor. With several different variables involved in why a bond may fail, it is important to understand what each failure is, and what can contribute to the failure occurring.
Substrate Failure
Substrate failure occurs when the adhesive bond is so strong that it causes at least one of the substrates to fail before the adhesive does.
In the packaging industry, this is commonly known as a fiber tear, due to how the substrate fails (tearing of the fibers that make up the box, leaving residue on one of the bonded substrates).
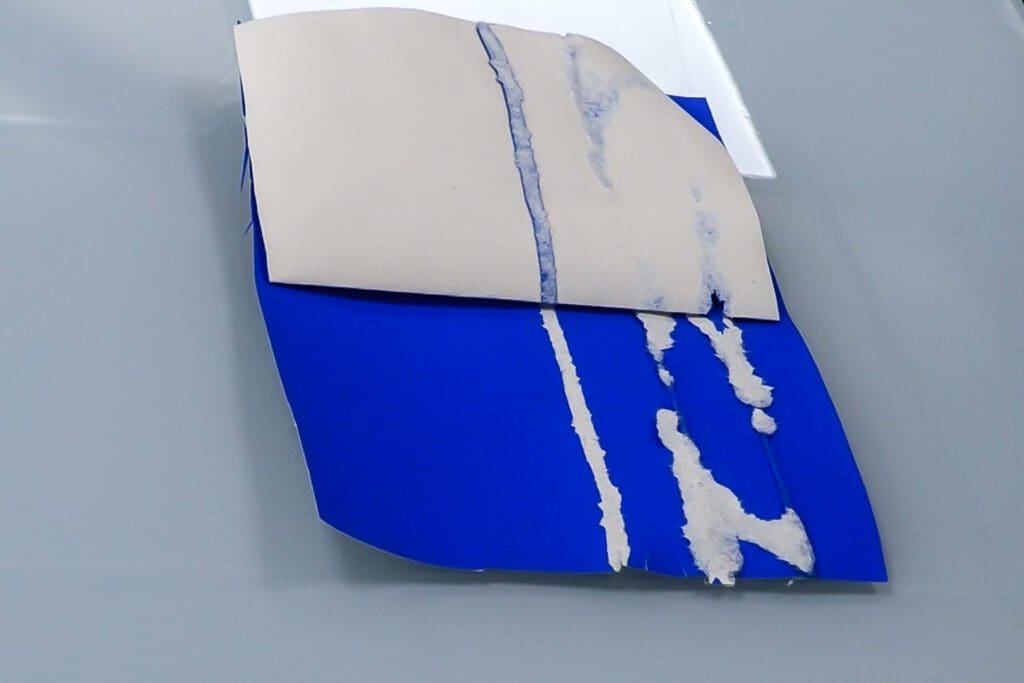
Despite this phrasing, fiber tear is not always present when substrate failure occurs. Materials such as glass and many hard plastics will break or crack when under pressure, which is also classified as substrate failure.
Many people assume that substrate failure means they need a stronger adhesive to stop the substrate from breaking. In reality, the adhesive used is strong enough to hold the material it has bonded to, so any material failure cannot be fixed by the adhesive.
In most circumstances, substrate failure is the desired goal, as it proves the adhesive has worked as it should.
Cohesive Failure
Cohesive failure happens when the adhesive has bonded well to both substrates, and the failure occurs internally within the adhesive itself.
The adhesive lacks sufficient cohesion to hold together, which causes it to separate, leaving residue adhesive on both substrates.

Cohesive failure commonly occurs when a soft-setting adhesive is used on very robust substrates, such as metal and thick plastics. If the material doesn’t fail, the internal strength of the adhesive reaches its limit, and the adhesive breaks.
Adhesive failure
Adhesive failure occurs when the adhesive hasn’t properly bonded to one of the substrates.
Several variables can trigger or affect adhesive failure; some are due to user error, while others are environmental factors. These can include a low application temperature, a low surface energy of the substrate being bonded, and a long process open time.
If the application temperature is too low, the adhesive may not have the same adhesive properties as it would when applied at the optimal temperature. This also subsequently affects the adhesives’ open time. If the substrates aren’t brought together quickly enough, the hot melt will have already started setting, minimising its adhesive qualities.
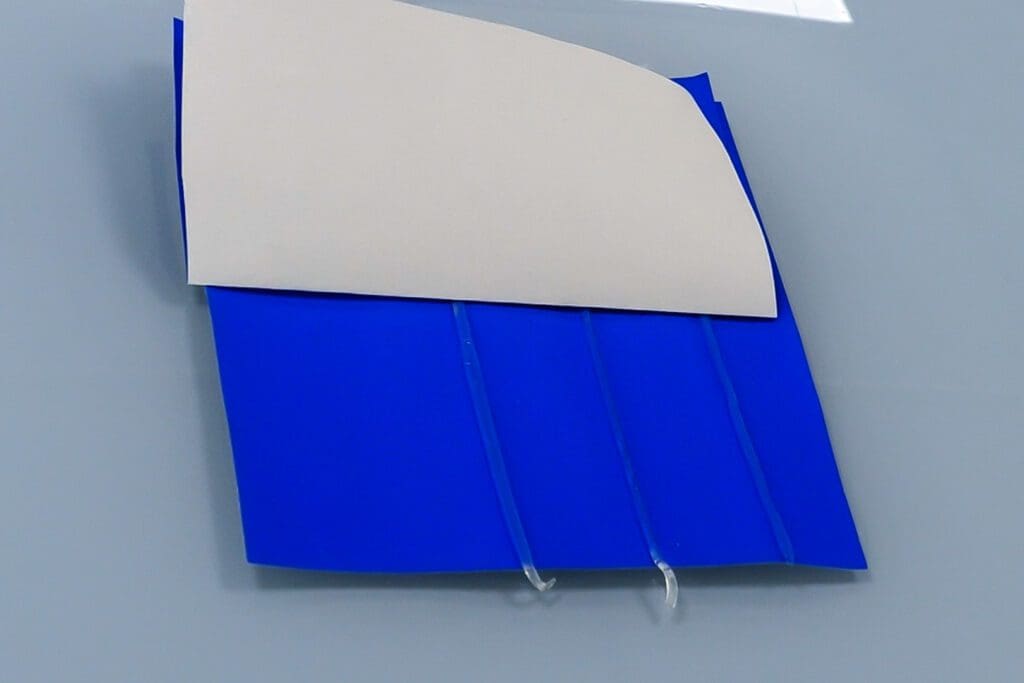
Low-surface-energy substrates such as polypropylene are notoriously difficult to effectively bond, with most hot melt adhesive formulations unable to spread across their surface and form chemical bonds. For more information about the difficulties of chemical bonding, read our blog post on physical and chemical bonding.
There are certain circumstances in which adhesive failure is beneficial to the product and how it works, for example, sticky notes. The adhesive on the reverse of sticky notes is designed to fail under the pressure of being pulled. If they didn’t experience adhesive failure, sticky notes could end up tearing under the force of being pulled away from a surface.
An example of a tecbond product that relies on eventual adhesive failure is peeltec 210. This grade is designed to form a temporary bond between substrates that is easily peelable when required. It is most commonly used to affix credit cards to letters and display labels on retail products.
The tecbond range of hot melt adhesives is formulated to suit the specific needs of the user and market application. Our adhesives have been used for over 40 years across a number of industries, including packaging, construction, product assembly, flooring, automotive, and hobby and craft.
For more information about the tecbond range, including finding the right adhesive for your business, contact our sales team.
+44 (0)1268 885 801
Leave a Reply