43mm hot melt adhesives: Why should you use them?
For over 40 years, Power Adhesives has been producing hot melt adhesive formulations in 43mm diameter slugs.
But why would you need 43mm slugs? What applications are they most beneficial for? And why should you choose to use 43mm adhesives over the traditional 12mm sticks?
Output
Looking to increase overall adhesive output? Then opt for a larger adhesive diameter! Certain industries and applications require a greater amount of adhesive per trigger pull, and 12mm glue guns can only provide a certain amount of adhesive, no matter how efficient the tool is.
Changing to 43mm hot melts allows the use of a bigger glue gun with more powerful heating systems and more efficient technology. This, in turn, results in a faster melt rate and increased output per kilogram.
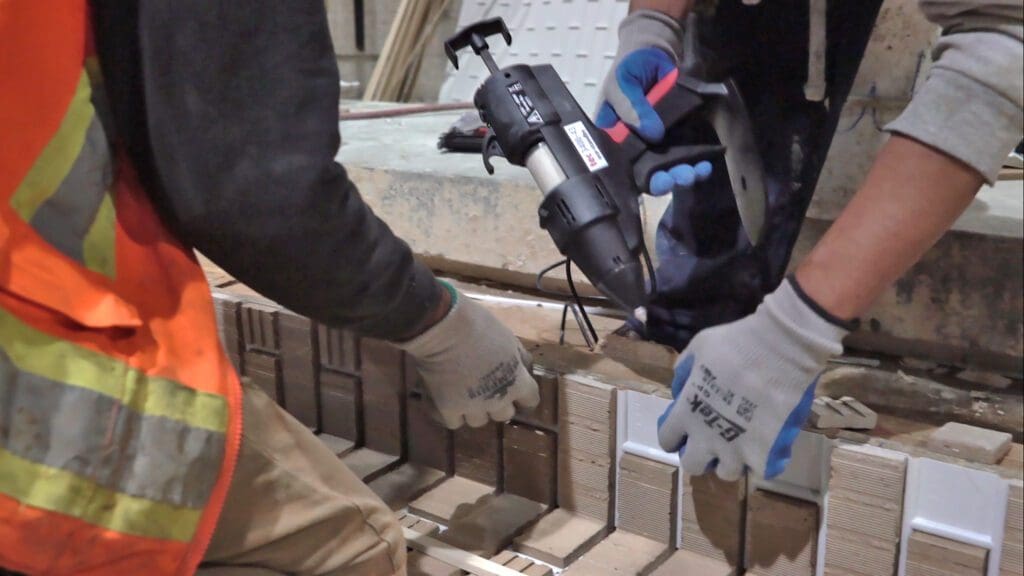
For example, the highest output 12mm tec glue gun dispenses around 2.5kg (5.5 lbs) of adhesive per hour. Contrast that with the entry-level 43mm tec glue gun, which dispenses around 3kg (6.5 lbs) per hour, with that output increasing with each more powerful tool up to the tec 7300, which has an output of 5.25kg (11.25 lbs) per hour.
Thanks to the impressive output 43mm adhesives provide, hot melts are now commonly used in both the foundry and precast industries, both demanding applications that require constant adhesive application in large quantities.
Spraying ability
It’s not just output that’s affected, as changing to 43mm adhesives opens up the range of tec spray applicators too. These spray tools not only increase adhesive coverage, but also enable adhesive formulations to be used on heat-sensitive substrates that can burn or melt when used with a regular hot melt glue gun.

Widely used in the product assembly and construction industries, formulations such as spraytec 410 and 420 aren’t available in 12mm sticks as their intended application requires a higher volume of adhesive to speed up the overall bonding process.
New possible formulations
Depending on the raw material makeup of the adhesive, many hot melts won’t work as 12mm sticks as they won’t hold together in smaller formats. Many grades, like tecbond 263, are only available in 43mm slugs, as their chemical makeup means the final formulation is quite soft and malleable.
Attempting to produce a 12mm stick with a formulation that is too “soft” may potentially damage the equipment it’s used with. Some of these issues include stick warping, stick breakages, and adhesive meltback, which in turn affect the performance of the extruded adhesive and how it bonds.
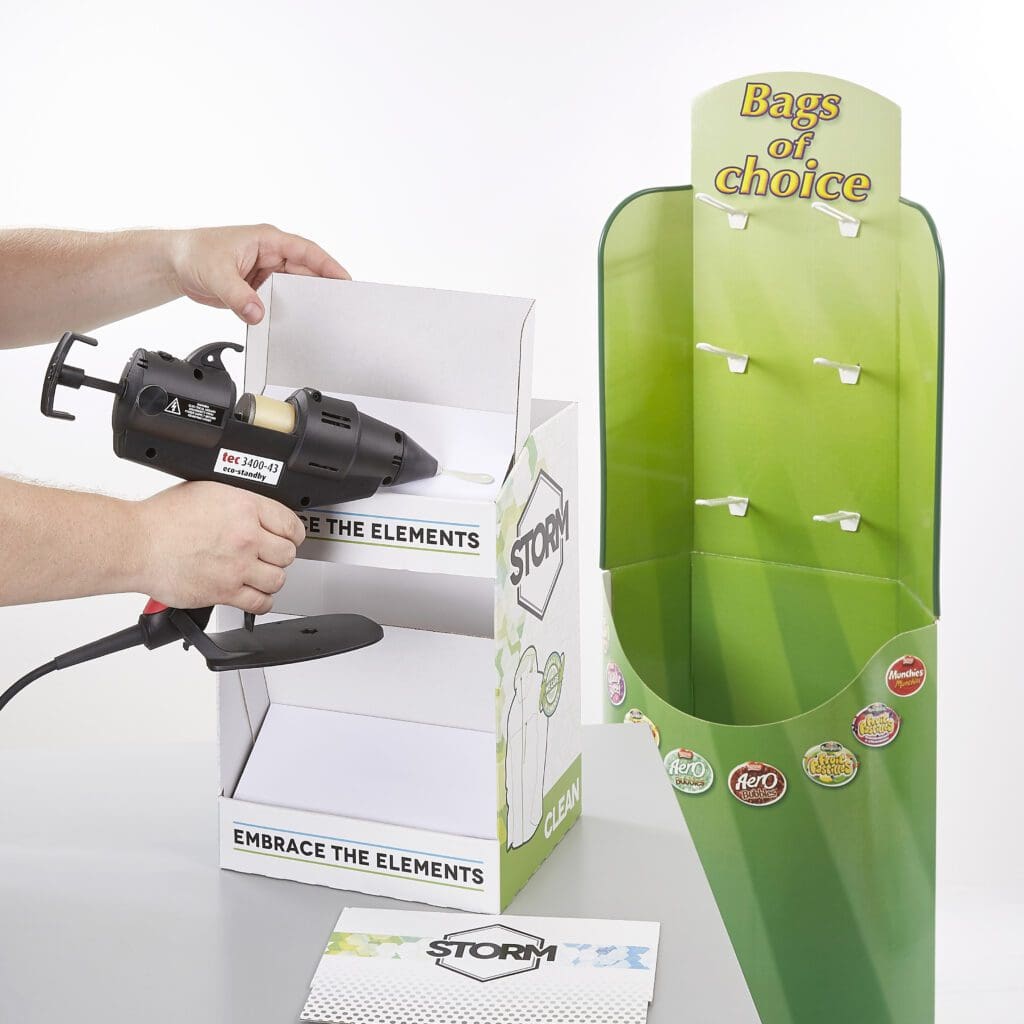
43mm slugs counter this issue, as the greater amount of glue results in an overall stronger slug. Think of it like this: you’re able to rip a piece of paper but cannot rip an entire catalogue; the same principle applies to the hot melt.
Conclusion
43mm hot melt slugs are the ideal adhesives for high-powered industries that need a constant supply of adhesive or need access to formulations that aren’t available in traditional 12mm sticks.
Since we started producing 43mm adhesives over 40 years ago, we have been constantly developing new formulations and updating glue gun technology to make these adhesives perform at their highest potential.
Created as part of a complete hot melt system, our 43mm adhesives work best with our range of 3000, 6000, and 7000 series of applicators. Tools such as the 3400 come with a range of temperature modules, so you can dispense glue at the exact temperature needed for the application.
If you’re looking to switch to 43mm adhesives, speak to one of our sales team about switching over and discovering the benefits for yourself.
+44 (0)1268 885 801