The Versatility of Hot Melt Adhesives: Beyond Crafts
Hot melt adhesives are intrinsic to many industries and how they operate. In many circumstances, hot melts promote greater efficiency, increased output and safer working environments.
Despite this, hot melt adhesives seem to carry the preconception that they’re mainly for craft or hobby purposes. But what if we told you that they could be used for everything from sealing boxes on a production line, to attaching cables, assembling oil filters, and more?
At Power Adhesives, we’re on a mission to educate as many people as we can so that more industry users can recognise the benefits of using hot melt adhesives over other adhesive systems.
What is a hot melt adhesive?
We have a more in-depth blog going into everything you need to know about hot melts, but as a starting point, a hot melt adhesive is a thermoplastic adhesive that forms bonds through melting and solidifying as opposed to drying like cyanoacrylates (super glues) and solvent-based adhesives (spray mounts).
The main benefits of hot melts are their fast bonding and setting speeds, combined with environmental benefits. In most circumstances, a hot melt adhesive will provide a near-instant hold between substrates. Although this initial bond won’t be at its strongest until several hours later, most bonds will be resistant to small movements between the materials, allowing these parts to progress along the assembly process.
As for the environmental benefits, hot melt adhesives are 100% solid content and are VOC-free (volatile organic compounds). This not only reduces overall waste, but allows operators to use them without the need for any respiratory PPE.
So what industries and applications are they used in?
Beyond crafting, hot melts are prevalent in a variety of different industries, covering applications great and small. Below are just some of the diverse applications hot melts are used for:
Packaging Solutions – Paper, Cardboard and Plastics
One of the more common uses for hot melt adhesives thanks to their cost-effectiveness and reliability, hot melts have been used for securing cartons and packaging inserts for over 50 years.
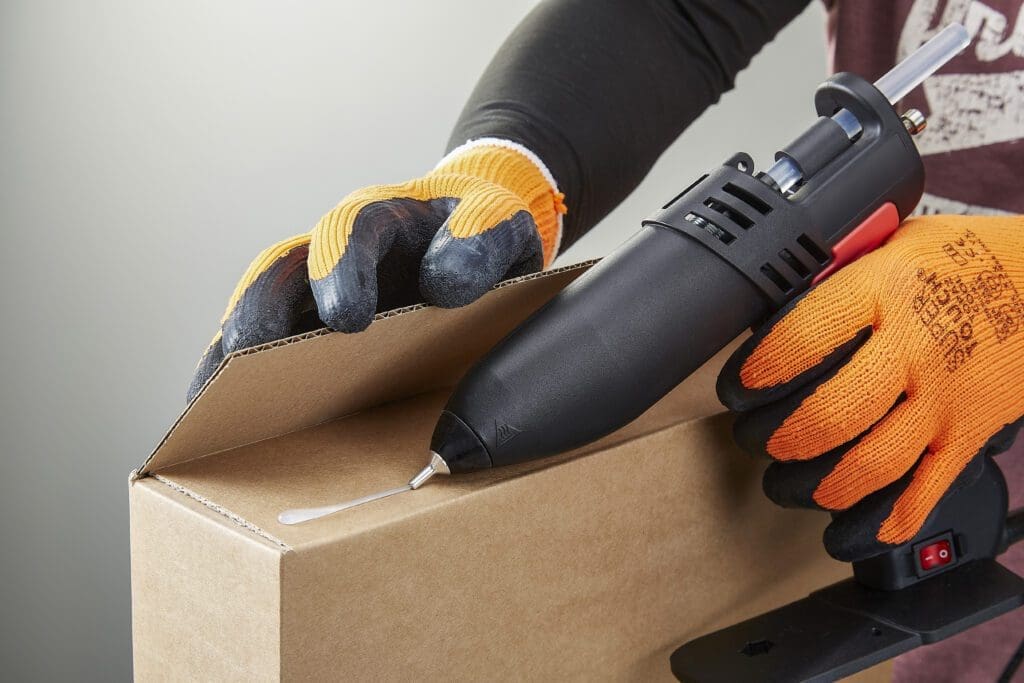
Alongside being more dependable than tapes or staples, hot melt adhesives provide a tamper-proof seal for cardboard boxes and will even work on more difficult substrates including triwall cardboard and varnished surfaces, most commonly found in food and retail POS packaging.
Plastics – Automotive to Electronics
As hot melt technology improves, so does its bonding potential. Plastics are particularly difficult to bond due to being very “low surface” causing adhesives to reticulate (gather upon themselves to avoid contact with the substrate) and therefore, decrease their ability to bond.
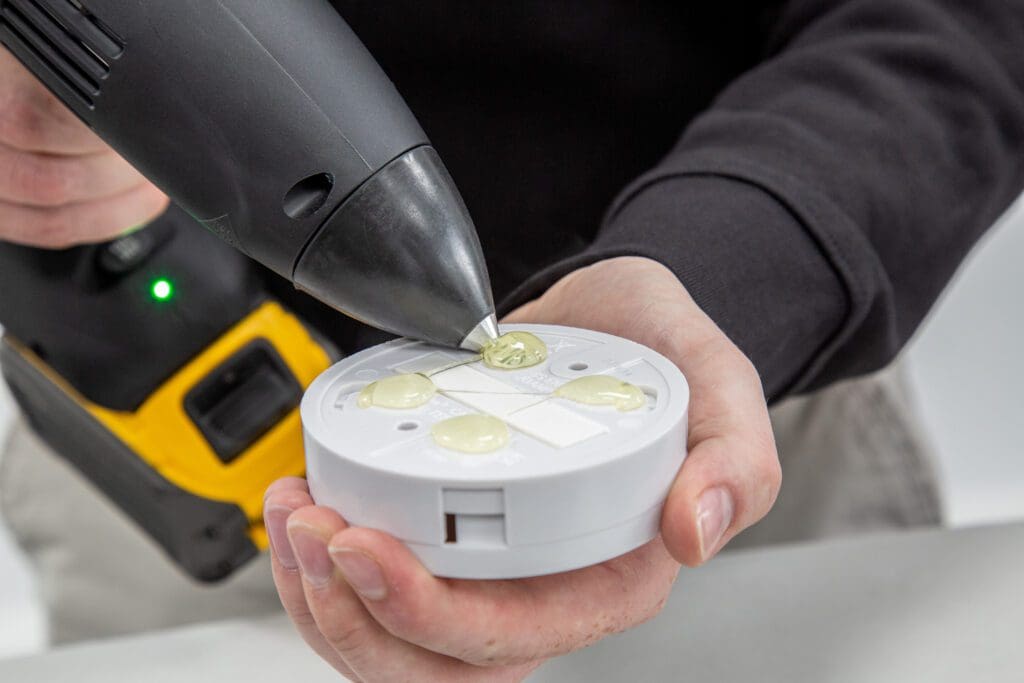
However, many grades in the Tecbond range have been specifically formulated to bond so-called “shiny” surfaces and offer a less-destructive alternative to screws and bolts. Some of these applications include:
- Interior trim on automobiles
- Internal electrical components (trunking, junction boxes, alarms and sensors etc)
- Electrical cabling
- White goods (assembly of fridges, freezers, washing machines etc)
- Assembly applications involving polypropylene
Woodworking – The alternative to wood glue
A vast majority of wood products, whether they’re mass-produced or hand-made, will have construction points held together with a traditional wood glue. These solvent-based solutions have long drying times, contain VOCs and tend to cure in the bottle if not used within a certain time frame.
Switching to hot melt adhesives eliminates all the issues involved with solvent-based adhesives by offering long or short open times to suit the application, near-instant initial bonds, and rapid setting speeds, all of which increase production rates.

Some of the most common places to find hot melt adhesives in wood applications include:
- Furniture construction
- Flooring installation
- Trim application
- Small joinery projects
- Internal household hardwood products (cabinets, bookshelves, coffee tables etc)
- Upholstery
For more demanding applications, hot melt adhesives can be used in conjunction with nails and pins to provide a more robust join.
Textiles – From handbags to high-heels
Many clothing and accessory manufacturers, including designer brands, are choosing to use hot melts over regular stitching or other fabric adhesives, thanks to their ability to provide long-lasting bonds across a variety of different materials.

Hot melts are crucial to many manufacturers as the bond is often not visible, and is flexible enough to allow for regular movements of wear and use that clothing goes through. Tecbond hot melts are already used in clothing applications such as:
- Shoes – Soles and insoles
- Handbags – inner fabric and accessory attachment
- Clothing interlining
- Underwear – Seam and lining bonding
Sensitive Substrates – Foams, polystyrene and polyethylene plastics
You may think that a hot melt adhesive’s downfall is its inability to work with heat-sensitive materials. However, certain hot melts are specifically formulated to melt and bond at lower temperatures – without damaging the material it’s designed to bond.
Alongside these low melt grades, at Power Adhesives, we manufacture specialist sprayable hot melts. These adhesives work together with Tec spray applicators to dispense hot melt in a spiral pattern. These adhesives cool much faster than a traditional bead application, and therefore, make contact with substrates at a much lower temperature.
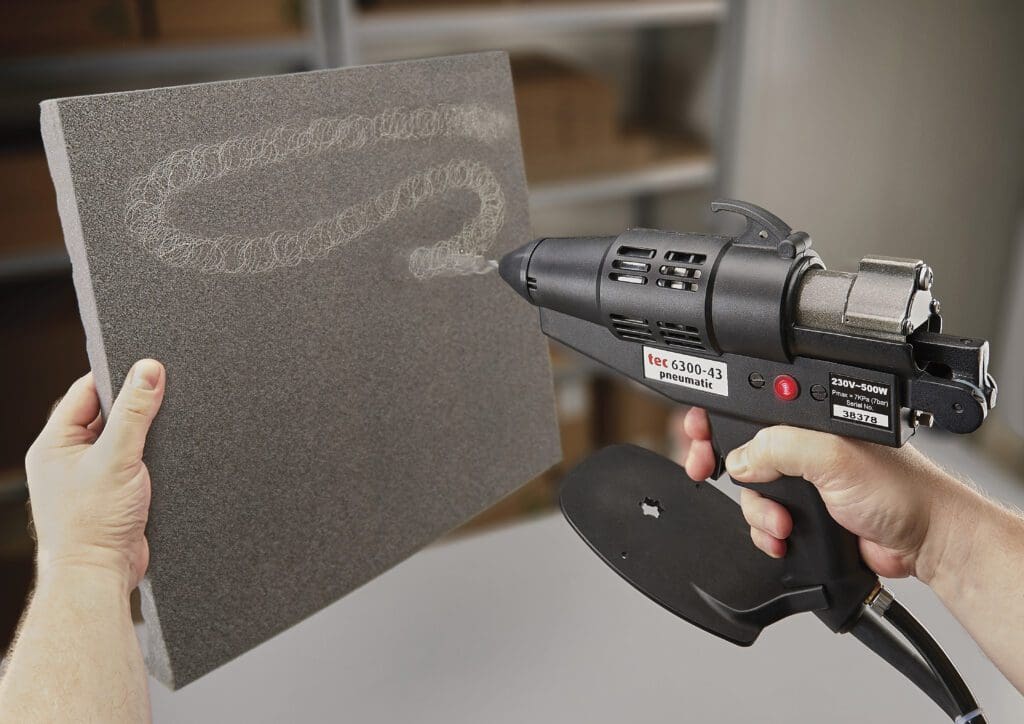
Low melt and sprayable formulations are used on many of the substrates and applications listed above, as well as:
- Furniture manufacturing – Cushions and seat padding
- Leather accessories – Purses & wallets
- Pallet Stabilisation – Alternative to shrink wrap on cartons and sacks
- Protective cases – Foam inserts
High Temperature & Chemical Rich Environments
The range of Tecbond hot melts features several grades that are polyamide-based. Polyamide adhesives exhibit greater temperature and chemical resistance than EVA or polyolefin-based formulations, which makes them the ideal adhesive for:
- Oil filters – Attaching pleated paper to the centre tube
- Electrical Potting & Encapsulation – Protecting sensitive electrical components
- Heating & Ventilation Systems
- Engine components

Despite their resistance, polyamide adhesives have the same characteristics as traditional hot melts, with variable open times depending on the formulation, and faster setting speeds (without the need for heating or extended compression periods).
Hot melt adhesive technology is constantly advancing, providing greater benefits not only to the user but also to the environment. Many Tecbond formulations, for example, are non-toxic and made from up to 44% bio-based materials, with a brand-new formulation being fully biodegradable.
Unlike many traditional bonding and fixing methods, hot melt adhesives offer versatility in areas where it’s more efficient and cost-effective to stick to one formulation for a variety of applications. Most hot melt adhesives have a near-infinite shelf life and can be used sparingly to further save the user money.
For more information on the Tecbond adhesive range, or to understand how hot melts could benefit your industry, contact our sales team.
+44 (0)1268 885 801
Leave a Reply