What to consider when choosing your hot melt adhesive grade
With hot melt adhesive technology constantly advancing and offering new solutions to a range of applications, new users need to understand what they’re looking for in their adhesive. It’s important to understand how different factors in the bonding process will affect the grade of hot melt you need. Below, we will detail some of the most important things to consider when choosing your hot melt adhesive grade.
Materials being bonded
This one is the most self-explanatory but also one of the most important factors to consider. Hot melts work by melting and then cooling, eventually solidifying to form a bond between substrates. This process uses both chemical and physical bonding, so it’s important to understand what bonding method your substrates require.
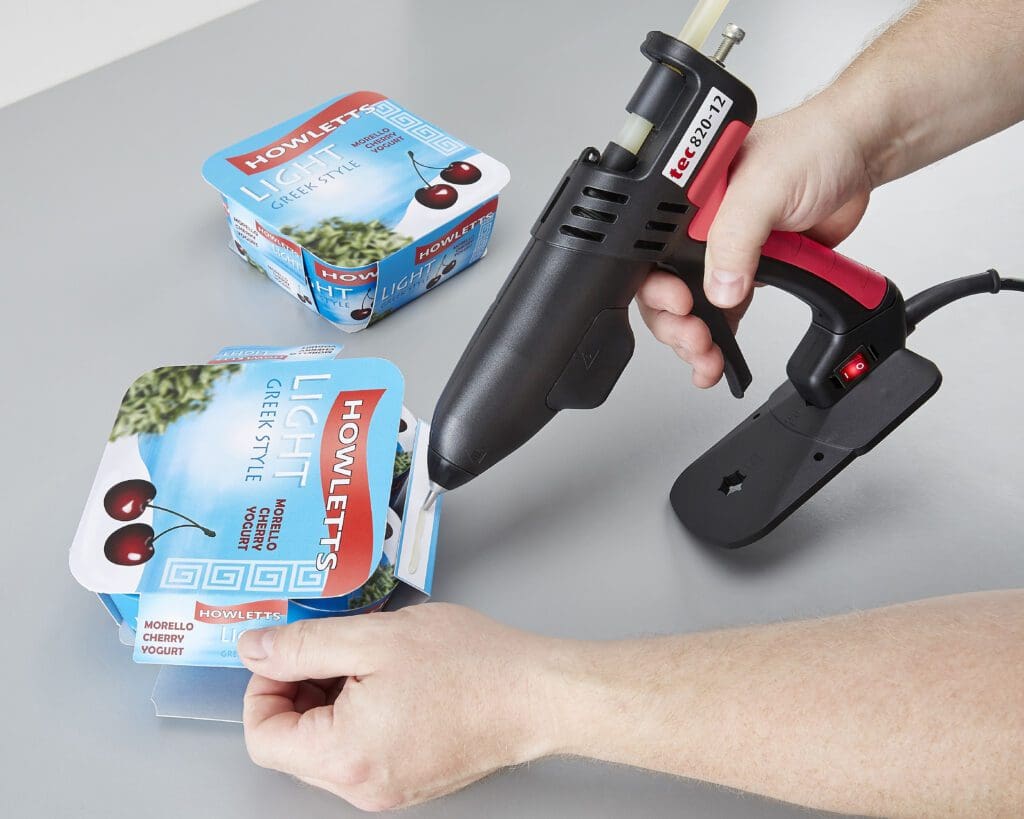
Materials like untreated wood, cardboard, paper, and fabrics will benefit from an adhesive with better physical bonding properties due to their porosity, whereas low-surface-energy materials like polyolefin plastics or glass will benefit from an adhesive with better chemical bonding properties. You can read more about chemical and physical bonding in our blog, explaining the difference between the two.
Tecbond’s hot melt adhesive range offers versatile solutions, with different grades capable of bonding almost any material, providing buyers with a reliable and adaptable option for their adhesive needs.
Working time and open time
These two go hand-in-hand, as working time will affect the open time required for the hot melt grade. Working time is the time it takes to complete the entire process of bonding materials together. Open time is the amount of time after application that the adhesive can still be manipulated.
If an adhesive’s open time is shorter than the working time, it will begin setting before compression, losing its tack and being unable to form a strong bond. This can then lead to adhesive failure. It is therefore important to find a hot melt adhesive with an open time longer than your working time.

In the packaging industry, manufacturers generally prefer shorter open times, as it means they can very quickly secure each box or carton and move on to the next one without requiring any clamping or holding. In contrast, product assembly applications may prefer a longer open time to accurately position the materials before compression.
So before purchasing a hot melt adhesive, it is important to understand how long it takes on average to bring your components together after the adhesive has been applied.
Temperature of the working environment
As mentioned previously, hot melt adhesives differ from water- and solvent-based solutions in their bonding method. With them needing to set, the temperature of the environment they’re used in will, in turn, affect their ability to set correctly.
The general rule is that the warmer the environment, the longer it will take for the bond to fully solidify, and vice versa. Using an incorrect hot melt adhesive can lead to soft bonds along with longer open times and setting speeds.
Certain hot melt grades will be designed for warmer conditions, while others are formulated to survive much lower temperatures. In many instances, this will affect their setting temperatures and softening points. This may not lead to adhesive or cohesive failure but may result in substrate movements due to the now softened bond.
Application temperature
This point is closely linked to materials being bonded. Specific substrates require a higher temperature to form a strong bond, while others require a lower temperature to avoid burning or melting.
Each hot melt formulation will have a recommended application temperature, which is linked to ideal performance. Running these hot melts at a higher or lower temperature may result in poor functionality in relation to its intended purpose.
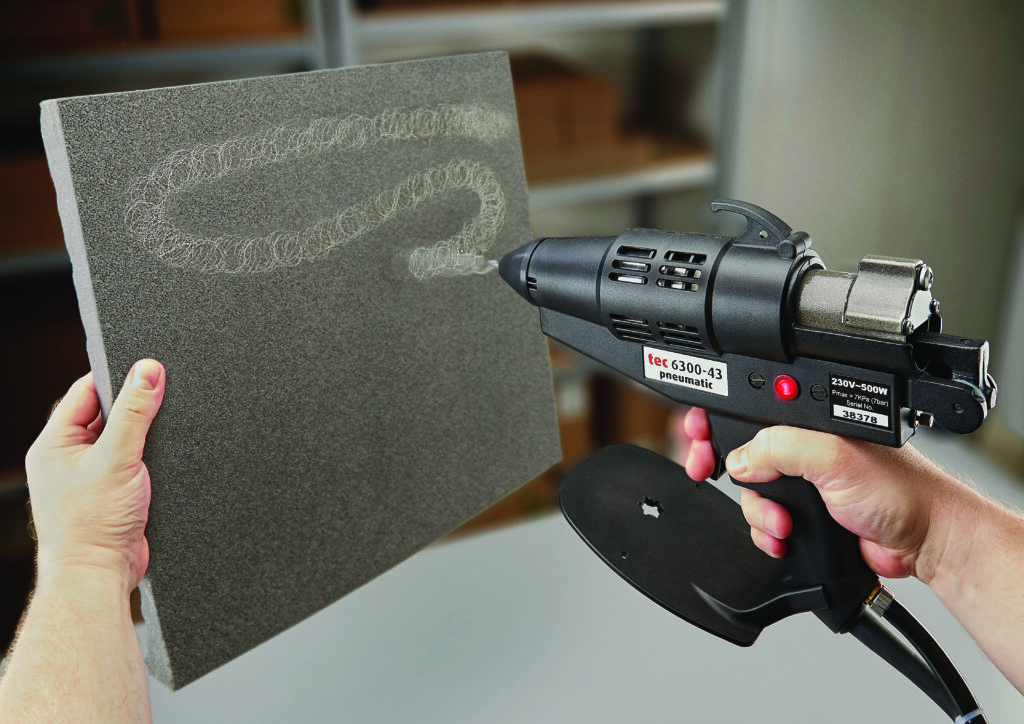
For example, tecbond low melt grades are formulated to run at 130°C. Dispensing them at regular hot melt temperatures (around 195°C) will make them very low viscosity and compromise their bonding ability. Conversely, running a high-temperature grade such as tecbond 7784 at a lower temperature will hinder its performance as a higher heat results in more energy being available for bonding.
Adhesive size
More specific to the tecbond range of hot melts, the size of the adhesive will affect not only the formulation you can use but also the type of applicator you need.
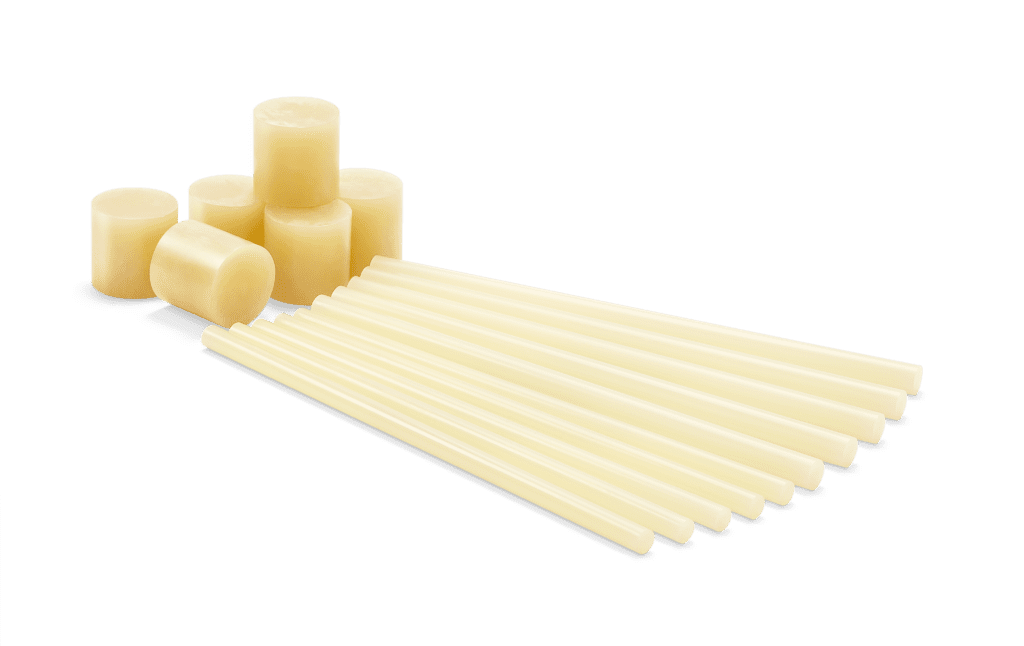
Tecbond 43mm adhesives allow users to improve their adhesive output while allowing for varied formulations that wouldn’t work in a traditional 12mm stick. Tecbond grades 265, 266, and 267 are only available in 43mm slugs, as their raw material makeup makes them too soft in a 12 or 15mm stick format.
For more technical information about the tecbond adhesive range or to find out what tecbond grade is most suitable for your application, please contact our sales team.
+44 (0)1268 885 801
Leave a Reply