Three advantages of using hot melt adhesives for woodworking
The tecbond range of adhesives features many grades suitable for woodworking applications, with some specializing in bonding specific types of wood. Compared to traditional water-based or polyurethane wood glues, tecbond hot melt adhesives offer users a simple and effective solution to common bonding problems raised by woodworking applications.
Setting times
Most forms of wood glue, whether water-based or polyurethane-based, recommend clamping newly bonded materials and leaving them to dry for 30 to 60 minutes before moving or continuing additional work. Not only does this increase overall working time, but depending on the size of the job, it also requires several clamps to hold the wood together and a dedicated area to leave the wood while the glue dries.
Hot melt adhesives are 100% solid content, meaning there is no drying or evaporating. They instead have a setting period where they cool and form a bond between the two substrates, whether this is through physical or chemical bonding. This means there is no need for extended clamping times to achieve a strong yet flexible bond.

Tecbond 23, one of the strongest woodworking and product assembly grades available, only requires a clamping time of around five minutes before the bond is strong enough to be moved without causing adhesive or cohesive failure. Many other tecbond woodworking adhesives, such as tecbond 5 and tecbond 213, only need to be held in place for several seconds before they adequately set, allowing the structure to be moved.
After only 24 hours, bonds made using tecbond adhesives will have reached their maximum strength. Other comparable woodworking adhesives recommend being left to dry for up to 48 hours to achieve maximum strength.
No expiry, no blocked nozzles
Tecbond adhesives eliminate the annoyance of blocked nozzles or a half-dried product that’s near impossible to apply. Unlike most wood adhesives, the tecbond range of woodworking hot melts are solid sticks that aren’t affected by environmental conditions. They have a near-unlimited shelf life, with no risk of drying out or warping to the point of being unusable.
Most water-based wood adhesives have a maximum shelf life of around one to two years before bacteria begin to grow in them. This usually results in the adhesive turning solid and, in some instances, starting to smell.
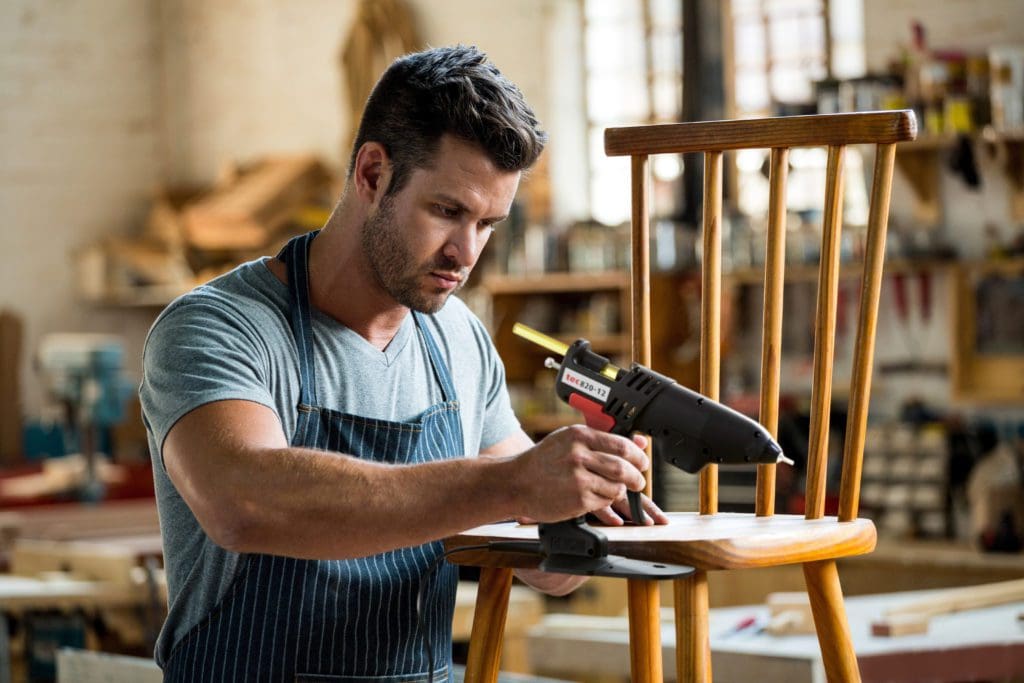
These adhesives are also prone to freezing due to their water content, making them unusable in colder climates or winter conditions. Rather than changing their storage requirements to prevent this from happening, most users will tend to purchase a new adhesive if their current one shows signs of change or expiration.
Works when bonding wood to other materials
Many of the most popular wood glues are designed to only bond wood and struggle to bond any other substrate. Their high water content translates to lower viscosity, ensuring they flow into the porous surface of the wood. This generates lots of small physical bonds, something that isn’t possible with less porous materials such as metal and hard plastics.
Conversely, the range of tecbond hot melts, although formulated to work on specific substrates, will effectively bond a wide variety of materials. Grades like tecbond 23 and 213, although primarily woodworking grades, will also work on cardboard, ceramics, and fabric.
For more information on our range of woodworking grades, or if you would like to request a sample, please don’t hesitate to contact our sales team.
+44 (0)1268 885801
Leave a Reply